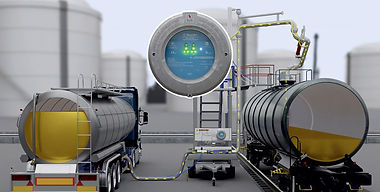
Earth Rite DGS System
Contact us at static@staticelectricity.com.au for a data sheet or to discuss your project in further detail.
The Earth-Rite DGS Dual Grounding System (DGS) has two independent ground monitoring circuits that allows operators to ground and continuously monitor two items of metal conductive plant equipment concurrently to less than 10 Ohms, such as two bulk transportation vehicles or other metallic vessels like Ex IBCs and metal drums.
This feature is commonly used to ground trucks and tank cars during transloading operations or to ground up to two trucks or tank cars that are being loaded/unloaded at dedicated loading rack installations.
Interlocking the grounding system with the process equipment being used enhances the safety and operating procedure before the process starts. If the ground is lost then Earth-Rite DGS can shut down the process for one or both of the channels.
![file[1].jpg](https://static.wixstatic.com/media/0a3978_2268af42a1954d58a764b224cf22f1a9~mv2.jpg/v1/fill/w_537,h_447,al_c,lg_1,q_80,enc_avif,quality_auto/file%5B1%5D.jpg)
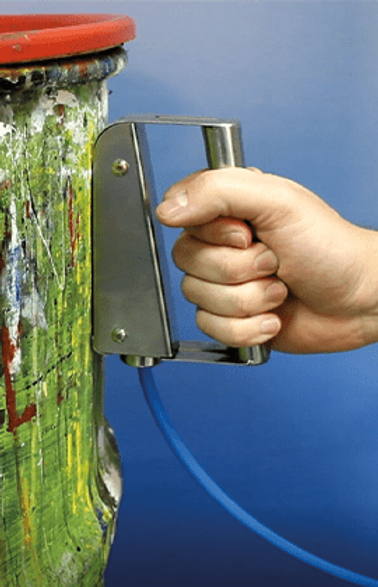

Clamps and Cables used for bonding and earthing purposes.
In some instances the clamps and cables used on site are the primary control employed to reduce the risk of static shock or fire and explosions.
It is important to understand the differences between each clamp and cable type and utilise the clamp and cable that is most appropriate.
​
Bonding clamps shall be electrically continuous from the teeth throughout the bonding clamp. Bonding clamps shall have a closing force such that they cannot be accidentally pulled off the equipment.
When a bonding clamp is required to bond to an object with an insulative surface layer, the clamp shall be capable of penetrating the insulative surface and making an electrical connection to the conductive part of the object under normal clamp pressure. Examples include bonding to a steel drum that is painted, coated or corroded.
When a bonding clamp is required to bond to an object subject to vibration, the clamp shall be capable of maintaining electrical contact when attached to vibrating equipment under normal clamp pressure. An example is bonding to a steel drum that is undergoing a mixing process.
NOTE Battery, welding and alligator type clamps typically do not satisfy these requirements.
​
The material that a clamp is made from is also important. Stainless Steel is one of the harder metals and is less likely to create issues of thermite reactions (sparks) when it comes in contact with less hard metals such as steel. Aluminium clamps, even if they have undergone a coating or hardenning process should not be used in environments where a thermite reaction is a possibility.
​
Typically clamps with teeth made from tungsten carbide should be used as they are most likely to penetrate coated surfaces on metal.
​
Clamps with teeth that are positioned "point to point" or "facing one another" should not be used on equipment under vibration. In this instance clamps with 2 teeth (side by side) are more suitable.

Cables used for mobile static bonds should be made of a steel braided or stainless-steel inner wire surrounded by a static dissipative outer cover. Where possible they should be spiral and they should not be typical standard electrical copper single core or multi strand.
If the cable is not coated in a static dissipative cover then static can accumulate on the surface of the outer cover.
Contact us at static@staticelectricity.com.au for a data sheet or to discuss your project in further detail.